Torque Sensor1 (C1511-C1514,C1517,C1521-C1523,C1528,C1531-C1555)
DESCRIPTION
While torque
sensor system, motor system or ECU system malfunctions are detected, the
fail-safe function suspends power assist. However, power assist
continues with limited assistance amount if only C1533 or C1534 is
output.
DTC No. | Detection Item |
DTC Detection Condition | Trouble Area |
Warning Indicate | Return-to-normal Condition |
Note |
C1511 |
Torque Sensor1 | Torque sensor malfunction |
Rack and pinion power steering gear assembly |
EPS warning light: Comes on |
Power switch is turned on (IG) again |
- |
C1512 |
Torque Sensor2 | Torque sensor malfunction |
Rack and pinion power steering gear assembly |
EPS warning light: Comes on |
Power switch is turned on (IG) again |
- |
C1513 |
Torque Sensor Deviation Excessive |
Torque sensor malfunction |
Rack and pinion power steering gear assembly |
EPS warning light: Comes on |
Power switch is turned on (IG) again |
- |
C1514 |
Torque Sensor Power Supply Voltage |
Torque sensor malfunction |
Rack and pinion power steering gear assembly |
EPS warning light: Comes on |
Power switch is turned on (IG) again |
- |
C1517 |
Torque Hold | Torque sensor malfunction |
Rack and pinion power steering gear assembly |
EPS warning light: Comes on |
Power switch is turned on (IG) again |
- |
C1521 |
Short in Motor Circuit |
Motor overcurrent | Rack and pinion power steering gear assembly |
EPS warning light: Comes on |
Power switch is turned on (IG) again |
- |
C1522 |
Power Supply Sensor | Motor current sensor malfunction |
Rack and pinion power steering gear assembly |
EPS warning light: Comes on |
Power switch is turned on (IG) again |
- |
C1523 |
Current Deviation Excessive |
Excessively large current deviation |
Rack and pinion power steering gear assembly |
EPS warning light: Comes on |
Power switch is turned on (IG) again |
- |
C1528 |
Motor Rotation Angle Sensor |
Motor rotation angle sensor malfunction |
Rack and pinion power steering gear assembly |
EPS warning light: Comes on |
Power switch is turned on (IG) again |
- |
C1531 |
ECU Malfunction | ECU internal malfunction (CPU malfunction) |
Rack and pinion power steering gear assembly |
EPS warning light: Comes on |
Power switch is turned on (IG) again |
- |
C1532 |
ECU Malfunction | ECU internal malfunction (Peripheral circuit malfunction) |
Rack and pinion power steering gear assembly |
EPS warning light: Comes on |
Power switch is turned on (IG) again |
- |
C1533 |
Temperature Sensor Circuit is Low or High |
ECU internal malfunction (Substrate temperature sensor malfunction) |
Rack and pinion power steering gear assembly |
EPS warning light: Comes on |
The ECU judges the system has returned to normal |
- |
C1534 |
EEPROM | ECU internal malfunction (EEPROM error) |
Rack and pinion power steering gear assembly |
EPS warning light: Comes on |
Power switch is turned on (IG) again |
- |
C1555 |
Motor Relay Welding Failure |
Motor relay circuit malfunction |
Rack and pinion power steering gear assembly |
EPS warning light: Comes on |
Power switch is turned on (IG) again |
- |
CAUTION / NOTICE / HINT
NOTICE:
If
the rack and pinion power steering gear assembly has been replaced,
perform assist map writing and torque sensor zero point calibration.
Click here
PROCEDURE
(a) Clear the DTCs.
Chassis > EMPS > Clear DTCs
(b) Check for DTCs.
Chassis > EMPS > Trouble Codes
Result | Proceed to |
DTCs
other than C1511, C1512, C1513, C1514, C1517, C1521, C1522, C1523,
C1528, C1531, C1532, C1533, C1534 or C1555 are not output. |
A |
DTCs other than C1511, C1512, C1513, C1514, C1517, C1521, C1522, C1523, C1528, C1531, C1532, C1533, C1534 or C1555 are output. |
B |
DTCs are not output. |
C |
A |
| REPLACE RACK AND PINION POWER STEERING GEAR ASSEMBLY |
B |
| GO TO DIAGNOSTIC TROUBLE CODE CHART |
C |
| USE SIMULATION METHOD TO CHECK |
Torque Sensor Zero Point Adjustment Undone (C1515)
DESCRIPTION
This DTC does
not indicate a malfunction. The power steering ECU (rack and pinion
power steering gear assembly) stores this DTC when it determines that
torque sensor zero point calibration has not been performed.
When the IG terminal voltage is below 8 V, torque sensor zero point calibration cannot be performed.
DTC No. | Detection Item |
DTC Detection Condition | Trouble Area |
Warning Indicate | Return-to-normal Condition |
Note |
C1515 |
Torque Sensor Zero Point Adjustment Undone |
This DTC is stored when torque sensor zero point calibration has not been performed. |
Torque sensor zero point calibration |
EPS warning light: Comes on |
Zero point calibration is performed or the power switch is turned on (IG) again |
There is no malfunction if this DTC is not output again after performing zero point calibration. |
CAUTION / NOTICE / HINT
NOTICE:
If
the rack and pinion power steering gear assembly has been replaced,
perform assist map writing and torque sensor zero point calibration.
Click here
PROCEDURE
(a) Calibrate the torque sensor zero point. (Step 1)
Chassis > EMPS > Utility
Tester Display |
Torque Sensor Adjustment |
(b) Check for DTCs. (Step 2)
Chassis > EMPS > Trouble Codes HINT:
If DTCs are output, perform steps (1) and (2) two more times.
Result | Proceed to |
DTCs are still output after performing steering zero point calibration 3 times. |
A |
Normal system code is output. |
B |
A |
| REPLACE RACK AND PINION POWER STEERING GEAR ASSEMBLY |
B |
| END |
Torque Sensor Zero Point Adjustment Incomplete (C1516)
DESCRIPTION
This DTC does
not indicate a malfunction. The power steering ECU (rack and pinion
power steering gear assembly) stores this DTC when it determines that
torque sensor zero point calibration has not completed.
DTC No. | Detection Item |
DTC Detection Condition | Trouble Area |
Warning Indicate | Return-to-normal Condition |
Note |
C1516 |
Torque Sensor Zero Point Adjustment Incomplete |
Torque sensor zero point calibration is incomplete due to the steering wheel being touched during calibration. |
Torque sensor zero point calibration |
EPS warning light: Comes on |
The DTC is cleared | There
is no malfunction if this DTC is not output again after clearing the
DTC and torque sensor calibration value, and performing zero point
calibration. |
CAUTION / NOTICE / HINT
NOTICE:
If
the rack and pinion power steering gear assembly has been replaced,
perform assist map writing and torque sensor zero point calibration.
Click here
PROCEDURE
(a) Clear the DTCs. (Step 1)
Chassis > EMPS > Clear DTCs
(b) Calibrate the torque sensor zero point. (Step 2)
Chassis > EMPS > Utility
Tester Display |
Torque Sensor Adjustment |
(c) Check for DTCs. (Step 3)
Chassis > EMPS > Trouble Codes HINT:
If DTCs are output, perform steps (1) to (3) two more times.
Result | Proceed to |
DTCs are still output after performing steering zero point calibration 3 times. |
A |
Normal system code is output. |
B |
A |
| REPLACE RACK AND PINION POWER STEERING GEAR ASSEMBLY |
B |
| END |
Vehicle Speed Signal (C1541)
DESCRIPTION
The power
steering ECU (rack and pinion power steering gear assembly) receives
vehicle speed signals from the skid control ECU (brake booster with
master cylinder assembly) via CAN communication. The ECU provides
appropriate assist force in accordance with the vehicle speed based on
the signals.
DTC No. | Detection Item |
DTC Detection Condition | Trouble Area |
Warning Indicate | Return-to-normal Condition |
Note |
C1541 |
Vehicle Speed Signal | A vehicle speed signal malfunction is detected |
- Brake control system
- CAN communication system
| EPS warning light: Comes on |
The ECU judges the system has returned to normal |
- |
CAUTION / NOTICE / HINT
NOTICE:
If
the rack and pinion power steering gear assembly has been replaced,
perform assist map writing and torque sensor zero point calibration.
Click here
PROCEDURE
1. |
CHECK CAN COMMUNICATION SYSTEM |
(a) Check if DTC U0129 is output.
Chassis > EMPS > Trouble Codes
Result | Proceed to |
DTC U0129 is not output. |
A |
DTC U0129 is output. |
B |
A |
| GO TO BRAKE CONTROL SYSTEM (DIAGNOSTIC TROUBLE CODE CHART) |
B |
| GO TO CAN COMMUNICATION SYSTEM (HOW TO PROCEED WITH TROUBLESHOOTING) |
IG Power Supply Voltage (C1551)
DESCRIPTION
When a malfunction is detected in the power source circuit, the fail-safe function suspends power assist.
DTC No. | Detection Item |
DTC Detection Condition | Trouble Area |
Warning Indicate | Return-to-normal Condition |
Note |
C1551 |
IG Power Supply Voltage |
When the PIG power supply voltage is normal, the IG power supply voltage is 18.5 V or higher |
- Harness or connector
- Rack and pinion power steering gear assembly
| EPS warning light: Comes on |
The ECU judges the system has returned to normal |
- |
WIRING DIAGRAM
CAUTION / NOTICE / HINT
NOTICE:
- If the rack and pinion power steering gear assembly has been replaced,
perform assist map writing and torque sensor zero point calibration.
Click here
- Inspect the fuses for circuits related to this system before performing the following procedure.
PROCEDURE
1. | CHECK HARNESS AND CONNECTOR (AUXILIARY BATTERY - RACK AND PINION POWER STEERING GEAR ASSEMBLY) |
(a) Disconnect the C67 rack and pinion power steering gear assembly connector.
*a | Front view of wire harness connector (to Rack and Pinion Power Steering Gear Assembly) |
- | - |
(b) Measure the voltage according to the value(s) in the table below.
Standard Voltage:
Tester Connection | Condition |
Specified Condition |
C67-4 (IG) - Body ground |
Power switch on (IG) |
Below 18.5 V |
NG |
| REPAIR OR REPLACE HARNESS OR CONNECTOR |
OK |
| |
(a) Clear the DTCs.
Chassis > EMPS > Clear DTCs
(b) Check for DTCs.
Chassis > EMPS > Trouble Codes
Result | Proceed to |
DTC is output. | A |
DTC is not output. | B |
A |
| REPLACE RACK AND PINION POWER STEERING GEAR ASSEMBLY |
B |
| USE SIMULATION METHOD TO CHECK |
PIG Power Supply Voltage (C1552,C1554)
DESCRIPTION
When a
malfunction is detected in the PIG power source and power supply relay
system, the fail-safe function suspends power assist.
DTC No. | Detection Item |
DTC Detection Condition | Trouble Area |
Warning Indicate | Return-to-normal Condition |
Note |
C1552 |
PIG Power Supply Voltage |
PIG power source circuit malfunction |
- EPS fuse
- Harness or connector
- Rack and pinion power steering gear assembly
| EPS warning light: Comes on |
Power switch is turned on (IG) again |
- |
C1554 |
Power Supply Relay Failure |
Power source relay circuit malfunction |
- EPS fuse
- Harness or connector
- Rack and pinion power steering gear assembly
| EPS warning light: Comes on |
Power switch is turned on (IG) again |
- |
WIRING DIAGRAM
CAUTION / NOTICE / HINT
NOTICE:
- If the rack and pinion power steering gear assembly has been replaced,
perform assist map writing and torque sensor zero point calibration.
Click here
- Inspect the fuses for circuits related to this system before performing the following procedure.
PROCEDURE
1. | CHECK HARNESS AND CONNECTOR (RACK AND PINION POWER STEERING GEAR ASSEMBLY - BODY GROUND) |
(a) Disconnect the C67 rack and pinion power steering gear assembly connector.
*a | Front view of wire harness connector (to Rack and Pinion Power Steering Gear Assembly) |
- | - |
(b) Measure the voltage according to the value(s) in the table below.
Standard Voltage:
Tester Connection | Condition |
Specified Condition |
C67-8 (PIG) - Body ground |
Always | 9 to 16 V |
(c) Measure the resistance according to the value(s) in the table below.
Standard Resistance:
Tester Connection | Condition |
Specified Condition |
C67-7 (PGND) - Body ground |
Always | Below 1 Ω |
OK |
| REPLACE RACK AND PINION POWER STEERING GEAR ASSEMBLY |
NG |
| REPAIR OR REPLACE HARNESS OR CONNECTOR |
Error in Matching of ECUs (C1567)
DESCRIPTION
The power
steering ECU (rack and pinion power steering gear assembly) determines
whether an incompatible hybrid vehicle control ECU, main body ECU
(multiplex network body ECU) or skid control ECU (brake booster with
master cylinder assembly) is installed based on the identification
information.
DTC No. | Detection Item |
DTC Detection Condition | Trouble Area |
Warning Indicate | Return-to-normal Condition |
Note |
C1567 |
Error in Matching of ECUs |
- An incompatible hybrid vehicle control ECU is detected
- An incompatible main body ECU (multiplex network body ECU) is detected
- An incompatible skid control ECU (brake booster with master cylinder assembly) is detected
|
- Incorrect hybrid vehicle control ECU
- Incorrect main body ECU (multiplex network body ECU)
- Incorrect skid control ECU (brake booster with master cylinder assembly)
- Rack and pinion power steering gear assembly
| EPS warning light: Comes on |
The ECU judges the system has returned to normal or the power switch is turned on (IG) again |
- |
CAUTION / NOTICE / HINT
NOTICE:
If
the rack and pinion power steering gear assembly has been replaced,
perform assist map writing and torque sensor zero point calibration.
Click here
PROCEDURE
(a) Confirm if the related part has the correct part number.
Related Part | Hybrid vehicle control ECU |
Main body ECU (Multiplex network body ECU) |
Skid control ECU (Brake booster with master cylinder assembly) |
NOTICE:
When removing the related part to check it, be sure to follow the appropriate procedures and precautions.
- Hybrid vehicle control ECU
Click here
- Main body ECU (Multiplex network body ECU)
Click here
- Skid control ECU (Brake booster with master cylinder assembly)
Click here
Result | Proceed to |
The related part has the correct part number. |
A |
The related part has an incorrect part number. |
B |
B |
| GO TO STEP 3 |
A |
| |
(a) Select Health Check on the Techstream screen and check if system DTCs of the related part are output.
HINT:
If
system DTCs of the related part are stored, assist map writing to the
power steering ECU (rack and pinion power steering gear assembly) may
not be performed properly.
Result | Proceed to |
System DTCs of the related part are output. |
A |
System DTCs of the related part are not output. |
B |
A |
| GO TO DIAGNOSTIC PROCEDURE INDICATED BY OUTPUT DTC |
B |
| REPLACE RACK AND PINION POWER STEERING GEAR ASSEMBLY |
3. |
REPLACE RELATED PART WITH PART THAT HAS CORRECT PART NUMBER |
(a) Replace the related part with one that has the correct part number.
- Hybrid vehicle control ECU
Click here
- Main body ECU (Multiplex network body ECU)
Click here
- Skid control ECU (Brake booster with master cylinder assembly)
Click here
NEXT |
| |
(a) Check for DTCs.
Chassis > EMPS > Trouble Codes
Result | Proceed to |
DTCs are not output. |
A |
DTCs are output. |
B |
A |
| END |
B |
| REPLACE RACK AND PINION POWER STEERING GEAR ASSEMBLY |
Assist Map Number Un-Writing (C1581)
DESCRIPTION
This DTC will
be stored if the power steering ECU (rack and pinion power steering gear
assembly) determines that the assist map is not written in the ECU.
DTC No. | Detection Item |
DTC Detection Condition | Trouble Area |
Warning Indicate | Return-to-normal Condition |
Note |
C1581 |
Assist Map Number Un-Writing |
Assist map not written in power steering ECU (rack and pinion power steering gear assembly) |
- CAN communication system
- Hybrid vehicle control ECU
- Main body ECU (Multiplex network body ECU)
- Skid control ECU (Brake booster with master cylinder assembly)
- Rack and pinion power steering gear assembly
| EPS warning light: Comes on |
Assist Map Writing is performed or the power switch is turned on (IG) again |
- |
CAUTION / NOTICE / HINT
NOTICE:
If
the rack and pinion power steering gear assembly has been replaced,
perform assist map writing and torque sensor zero point calibration.
Click here
HINT:
Related parts store information necessary for assist map writing.
Related Part:
- Hybrid vehicle control ECU
- Main body ECU (Multiplex network body ECU)
- Skid control ECU (Brake booster with master cylinder assembly)
PROCEDURE
1. | PERFORM ASSIST MAP WRITING |
(a) Perform assist map writing.
Chassis > EMPS > Utility
Tester Display |
Signal Check |
(b) Check for DTCs.
Chassis > EMPS > Trouble Codes
Result | Proceed to |
DTC C1581 is output. |
A |
DTC C1581 is not output. |
B |
B |
| END |
A |
| |
2. |
CHECK CAN COMMUNICATION SYSTEM |
(a) Check for DTCs.
Click here
Result | Proceed to |
CAN communication system DTCs are not output. |
A |
CAN communication system DTCs are output. |
B |
B |
| GO TO CAN COMMUNICATION SYSTEM |
A |
| |
(a) Confirm if the related part has the correct part number.
Related Part | Hybrid vehicle control ECU |
Main body ECU (Multiplex network body ECU) |
Skid control ECU (Brake booster with master cylinder assembly) |
NOTICE:
When removing the related part to check it, be sure to follow the appropriate procedures and precautions.
- Hybrid vehicle control ECU
Click here
- Main body ECU (Multiplex network body ECU)
Click here
- Skid control ECU (Brake booster with master cylinder assembly)
Click here
Result | Proceed to |
The related part has the correct part number. |
A |
The related part has an incorrect part number. |
B |
B |
| GO TO STEP 5 |
A |
| |
(a) Select Health Check on the Techstream screen and check if system DTCs of the related part are output.
HINT:
If
system DTCs of the related part are stored, assist map writing to the
power steering ECU (rack and pinion power steering gear assembly) may
not be performed properly.
Result | Proceed to |
System DTCs of the related part are output. |
A |
System DTCs of the related part are not output. |
B |
A |
| GO TO DIAGNOSTIC PROCEDURE INDICATED BY OUTPUT DTC |
B |
| REPLACE RACK AND PINION POWER STEERING GEAR ASSEMBLY |
5. |
REPLACE RELATED PART WITH PART THAT HAS CORRECT PART NUMBER |
(a) Replace the related part with one that has the correct part number.
- Hybrid vehicle control ECU
Click here
- Main body ECU (Multiplex network body ECU)
Click here
- Skid control ECU (Brake booster with master cylinder assembly)
Click here
NEXT |
| |
(a) Check for DTCs.
Chassis > EMPS > Trouble Codes
Result | Proceed to |
DTCs are not output. |
A |
DTCs are output. |
B |
A |
| END |
B |
| REPLACE RACK AND PINION POWER STEERING GEAR ASSEMBLY |
Assist Map Number Mismatch (C1582)
DESCRIPTION
When an
incorrect hybrid vehicle control ECU, main body ECU (multiplex network
body ECU) or skid control ECU (brake booster with master cylinder
assembly) is installed after the assist map has been written to the
power steering ECU (rack and pinion power steering gear assembly), DTC
C1582 is stored because the information stored in the power steering ECU
(rack and pinion power steering gear assembly) does not match the
vehicle specifications.
DTC No. | Detection Item |
DTC Detection Condition | Trouble Area |
Warning Indicate | Return-to-normal Condition |
Note |
C1582 |
Assist Map Number Mismatch |
Assist map number mismatch |
- CAN communication system
- Incorrect hybrid vehicle control ECU
- Incorrect main body ECU (multiplex network body ECU)
- Incorrect skid control ECU (brake booster with master cylinder assembly)
- Rack and pinion power steering gear assembly
| EPS warning light: Does not come on |
Assist Map Writing is performed or the power switch is turned on (IG) again |
- |
CAUTION / NOTICE / HINT
NOTICE:
If
the rack and pinion power steering gear assembly has been replaced,
perform assist map writing and torque sensor zero point calibration.
Click here
HINT:
Related parts store information necessary for assist map writing.
Related Part:
- Hybrid vehicle control ECU
- Main body ECU (Multiplex network body ECU)
- Skid control ECU (Brake booster with master cylinder assembly)
PROCEDURE
1. | CHECK CAN COMMUNICATION SYSTEM |
(a) Check for DTCs.
Click here
Result | Proceed to |
CAN communication system DTCs are not output. |
A |
CAN communication system DTCs are output. |
B |
B |
| GO TO CAN COMMUNICATION SYSTEM |
A |
| |
(a) Check if the part below has been replaced with an incorrect part in the past.
Related Part | Hybrid vehicle control ECU |
Main body ECU (Multiplex network body ECU) |
Skid control ECU (Brake booster with master cylinder assembly) |
NOTICE:
When removing the related part to check it, be sure to follow the appropriate procedures and precautions.
- Hybrid vehicle control ECU
Click here
- Main body ECU (Multiplex network body ECU)
Click here
- Skid control ECU (Brake booster with master cylinder assembly)
Click here
(b)
When DTC C1582 is output and parts have not been exchanged, replace the
power steering ECU (rack and pinion power steering gear assembly) as it
may have an internal malfunction.
NOTICE:
If the rack and pinion power steering gear assembly has been replaced, perform assist map writing.
Click here
Result | Proceed to |
The related part has an incorrect part number. |
A |
The
related part has the correct part number, or a related part and rack
and pinion power steering gear assembly have not been replaced. |
B |
B |
| REPLACE RACK AND PINION POWER STEERING GEAR ASSEMBLY |
A |
| |
3. |
REPLACE RELATED PART WITH PART THAT HAS CORRECT PART NUMBER |
(a) Replace the related part with one that has the correct part number.
- Hybrid vehicle control ECU
Click here
- Main body ECU (Multiplex network body ECU)
Click here
- Skid control ECU (Brake booster with master cylinder assembly)
Click here
NEXT |
| |
(a) Check for DTCs.
Chassis > EMPS > Trouble Codes
Result | Proceed to |
DTCs are not output. |
A |
DTCs are output. |
B |
A |
| END |
B |
| REPLACE RACK AND PINION POWER STEERING GEAR ASSEMBLY |
Calibration
CALIBRATION
TORQUE SENSOR ZERO POINT CALIBRATION (USING TECHSTREAM)
NOTICE:
Perform torque sensor zero point calibration if any of the following conditions occur:
- The rack and pinion power steering gear assembly has been replaced.
- There is a difference in steering effort between turning left and right.
(a) Perform inspection before calibration.
(1) Turn the power switch off.
(2) Connect the Techstream to the DLC3.
(3) Turn the power switch on (IG).
(4) Turn the Techstream on.
(5) Calibrate the rack and pinion power steering gear assembly. Enter the following menus: Chassis / EMPS / Data List.
(6) Read the Data List according to the display on the Techstream.
Chassis > EMPS > Data List
Tester Display | Measurement Item |
Range | Normal Condition |
Diagnostic Note |
IG Power Supply | IG power source voltage |
Min.: 0.0000 V Max.: 20.1531 V |
8 to 16 V | Power switch on (IG) |
Chassis > EMPS > Data List
Tester Display |
IG Power Supply |
Standard Voltage:
8 to 16 V
NOTICE:
If
the IG power supply voltage is 8 V or less, calibration cannot be
performed. In this case, charge or replace the auxiliary battery, and
then perform calibration.
(b) Perform torque sensor zero point calibration.
NOTICE:
If
DTC C1516 (Torque Sensor Zero Point Adjustment Incomplete) is stored,
the torque sensor zero point cannot be calibrated. Clear the DTCs before
starting calibration.
(1) Align the front wheels straight ahead and center the steering wheel.
(2) Turn the power switch off.
(3) Connect the Techstream to the DLC3.
(4) Turn the power switch on (IG).
(5) Turn the Techstream on.
(6) Enter the following menus: Chassis / EMPS / Utility / Torque Sensor Adjustment.
Chassis > EMPS > Utility
Tester Display |
Torque Sensor Adjustment |
NOTICE:
- Do not turn the steering wheel sharply.
- During the torque sensor zero point calibration the steering wheel will
shudder. Do not touch the steering wheel until at least 3 seconds have
elapsed after the shuddering has stopped.
(7) Check for DTCs.
Chassis > EMPS > Trouble Codes NOTICE:
If DTC C1515, C1516, C1534 or C1581 is output, perform troubleshooting for the corresponding DTC.
Result | See Procedure |
DTC C1515 is output. |
|
DTC C1516 is output. |
|
DTC C1534 is output. |
|
DTC C1581 is output. |
|
ASSIST MAP WRITING (USING TECHSTREAM)
NOTICE:
Perform assist map writing if the following condition occurs:
The rack and pinion power steering gear assembly has been replaced.
(a) Turn the power switch off.
(b) Connect the Techstream to the DLC3.
(c) Turn the power switch on (IG).
(d) Turn the Techstream on.
(e) Enter the following menus: Chassis / EMPS / Utility / Signal Check.
Chassis > EMPS > Utility
Tester Display |
Signal Check |
HINT:
- Follow the instructions on the Techstream to perform Signal Check.
- With DTC C1581 output, performing Signal Check will cause the rack and
pinion power steering gear assembly to enter Signal Check and the assist
map will be written automatically.
(f) Wait for at least 5 seconds.
(g) Check for DTCs.
Chassis > EMPS > Trouble Codes
HINT:
After writing the assist map, if DTC C1581 is output, perform the troubleshooting procedure for DTC C1581.
Click here
Check Assist Limit Record
CAUTION / NOTICE / HINT
HINT:
Perform this troubleshooting procedure when no DTCs are output, including DTCs related to CAN communication system malfunctions.
PROCEDURE
1. |
READ VALUE USING TECHSTREAM (ASSIST LIMIT RECORD 1) |
(a) Using the Techstream, read the Data List item "Assist Limit Record 1".
Click here
Chassis > EMPS > Data List
Tester Display | Measurement Item |
Range | Normal Condition |
Diagnostic Note |
Assist Limit Record 1 | Information of assist limit that was used in the past or is currently in use (latest history) |
Unrec,
Mtr Overheat, Pow Vol Low, Pow Vol Low Prevent, Eng Stall, Ready OFF,
Mtr Overload, DC-DC Malf, Vhcl Spd Sig Malf, Batt Vol Keep |
- | - |
HINT:
For the Data List item "Assist Limit Record 1", each item in the Range is described below.
|
Range | Description |
Diagnostic Note |
Assist Limit Record 1 | Unrec |
No assist limit. Continue with troubleshooting for "Heavy steering". |
- |
Mtr Overheat |
When
the vehicle is stopped or traveling at low speed, and steering
operations are performed repeatedly or the steering wheel is turned all
the way to the side and held there for a long time, assist may be
limited in order to prevent overheating of the power steering motor
assembly and power steering ECU assembly. After 10
minutes elapse with the power switch on (READY) and no steering
operations being performed, the system will return to normal. After recovering from the overheated condition, assist can be performed as usual. |
- |
Pow Vol Low |
When
insufficient auxiliary battery charge, or auxiliary battery degradation
etc. causes the voltage to temporarily decrease, assist may be stopped. After the auxiliary battery condition returns to normal, assist can be performed as usual. |
- |
Pow Vol Low Prevent |
When
insufficient auxiliary battery charge, or auxiliary battery degradation
etc. causes the voltage to temporarily decrease, assist may be limited. After the auxiliary battery condition returns to normal, assist can be performed as usual. |
- |
Eng Stall |
When the engine stalls, auxiliary battery charge becomes insufficient, so assist is stopped.
After recovering from the engine stall, assist can be performed as usual. |
Not displayed for this vehicle |
Ready OFF | After
Ready ON, if a malfunction in the HV system etc. causes a return to
Ready OFF, the HV battery charge becomes insufficient, so assist is
stopped. After returning to Ready ON state, assist can be performed as usual. |
- |
Mtr Overload |
When
the steering wheel cannot turn, such as when a road wheel is against a
curb, if the driver continues to apply force to the steering wheel,
current to the motor may be limited to prevent overheating. When the steering wheel is returned to a neutral position, assist can be performed as usual. |
- |
DC-DC Malf |
If there is a malfunction in the DC-DC converter, etc., assist may be limited.
After the DC-DC converter returns to normal, assist can be performed as usual. |
Not displayed for this vehicle |
Vhcl Spd Sig Malf | If the vehicle speed signal is abnormal due to a wheel speed sensor malfunction, etc., assist may be limited. |
- |
Batt Vol Keep |
When
insufficient auxiliary battery charge, or auxiliary battery degradation
etc. causes the voltage to temporarily decrease, assist may be limited. After the auxiliary battery condition returns to normal, assist can be performed as usual. |
- |
Chassis > EMPS > Data List
Tester Display |
Assist Limit Record 1 |
(b)
Based on the "Assist Limit Record 1" information, the following Data
List items and the information from the customer interview, explain the
situation to the customer.
Chassis > EMPS > Data List
Tester Display |
Record 1 Key Cycle |
Record 1 Key Cycle Elapsed Time |
HINT:
If
it is necessary to investigate further into the past, check the "Assist
Limit Record 2" and "Assist Limit Record 3" information in the same way
as "Assist Limit Record 1".
NEXT | |
END |
Data List / Active Test
DATA LIST / ACTIVE TEST
DATA LIST
HINT:
Using
the Techstream to read the Data List allows the values or states of
switches, sensors, actuators and other items to be read without removing
any parts. This non-intrusive inspection can be very useful because
intermittent conditions or signals may be discovered before parts or
wiring is disturbed. Reading the Data List information early in
troubleshooting is one way to save diagnostic time.
NOTICE:
In
the table below, the values listed under "Normal Condition" are
reference values. Do not depend solely on these reference values when
deciding whether a part is faulty or not.
(a) Turn the power switch off.
(b) Connect the Techstream to the DLC3.
(c) Turn the power switch on (IG).
(d) Turn the Techstream on.
(e) Enter the following menus: Chassis / EMPS / Data List.
(f) Read the Data List according to the display on the Techstream.
Chassis > EMPS > Data List
Tester Display | Measurement Item |
Range | Normal Condition |
Diagnostic Note |
Meter Vehicle Velocity |
Vehicle speed from speedometer |
Min.: 0.0 km/h (0.0 MPH) Max.: 300.0 km/h (186.4 MPH) |
- 0 km/h (0 MPH): Power switch on (READY) and vehicle stopped
- No significant fluctuation: Power switch on (READY) and vehicle driven at a constant speed
| - |
Wheel Speed Right | Rear right wheel speed |
Min.: 0 km/h (0 MPH) Max.: 255 km/h (158 MPH) |
- 0 km/h (0 MPH): Power switch on (READY) and vehicle stopped
- No significant fluctuation: Power switch on (READY) and vehicle driven at a constant speed
| - |
Wheel Speed Left | Rear left wheel speed |
Min.: 0 km/h (0 MPH) Max.: 255 km/h (158 MPH) |
- 0 km/h (0 MPH): Power switch on (READY) and vehicle stopped
- No significant fluctuation: Power switch on (READY) and vehicle driven at a constant speed
| - |
Motor Actual Current | Amount of current to motor |
Min.: -327.68 A Max.: 327.67 A |
Value changes in proportion to steering effort - The value increases when turning right and decreases when turning left |
Power switch on (READY) and steering wheel being turned |
Command Value Current | Requested current to motor |
Min.: -327.68 A Max.: 327.67 A |
Value changes in proportion to steering effort - The value increases when turning right and decreases when turning left |
Power switch on (READY) and steering wheel being turned |
Steering Angle Velocity |
Steering angle speed | Min.: -32768 deg/s
Max.: 32767 deg/s | Value changes in proportion to steering speed
- The value increases when turning left and decreases when turning right |
Power switch on (READY) and steering wheel being turned |
Thermistor Temperature |
ECU substrate temperature |
Min.: -50.0°C (-58.0°F) Max.: 150.0°C (302.0°F) |
-50°C to 150°C (-58°F to 302°F) |
- |
IG Power Supply |
IG power source voltage |
Min.: 0.0000 V Max.: 20.1531 V |
8 to 16 V | Power switch on (IG) |
Steering Angle Sens Sig |
Steering sensor signal state |
OK or NG(1) or NG(2) or NG(3) |
OK: Steering sensor signal received NG(1): The learning has not completed
NG(2): Steering sensor abnormal NG(3): Communication error |
- |
Steering Wheel Torque |
Steering wheel torque | Min.: -327.68 Nm
Max.: 7.00 Nm | Value changes in proportion to steering effort
- The value increases when turning left and decreases when turning right |
Power switch on (READY) and steering wheel being turned |
Motor Rotation Angle | Motor rotation angle |
Min.: 0.000 deg Max.: 1441.770 deg |
During steering operation, motor rotation angle value changes from 0 to 360° |
Power switch on (READY) and steering wheel being turned |
Command Val Current 2 | Requested current to motor |
Min.: -327.68 A Max.: 327.67 A |
Value changes in proportion to steering effort |
Power switch on (READY) and steering wheel being turned |
Motor Voltage | Motor power supply voltage |
Min.: 0.000 V Max.: 98.000 V |
- Approximately 27 V: Power switch on (READY) and steering wheel being turned
- Approximately 27 to 34 V: Power switch on (READY) and steering wheel not being turned
| - |
TRQ1 Zero Point Value | Zero point value of torque sensor 1 |
Min.: 0.0000 V Max.: 4.9725 V |
2.3 to 2.7 V | Power switch on (READY) and steering wheel not being turned (without load) |
TRQ2 Zero Point Value | Zero point value of torque sensor 2 |
Min.: 0.0000 V Max.: 4.9725 V |
2.3 to 2.7 V | Power switch on (READY) and steering wheel not being turned (without load) |
IG ON/OFF Times | Number of times of power switch turned on/off since latest DTC detection |
Min.: 0 times Max.: 65535 times |
- | - |
Motor Overheat Record | Continuous overheat prevention control record |
Unrec or Rec | Unrec |
Unrec: Unrecorded Rec: Recorded The
amount of power assist may be decreased to prevent the motor and ECUs
from overheating if the steering wheel is continuously turned when the
vehicle is either stopped or driven at a low speed, or if the steering
wheel is kept in either full lock position for a long time. |
Motor Lo Power Record | PIG power source voltage drop record |
Unrec or Rec | Unrec |
Unrec: Unrecorded Rec: Recorded If the PIG power source voltage decreases temporarily, the amount of power assist will be reduced. |
Eng Rev Inter Record | Record of engine signal interruption |
Unrec or Rec | Unrec |
Unrec: Unrecorded Rec: Recorded |
Str Angle Inter Record |
Record of steering sensor signal interruption occurrence display |
Unrec or Rec | Unrec |
Unrec: Unrecorded Rec: Recorded |
Spd Sig Invalid Record |
Record of vehicle speed signal invalid |
Unrec or Rec | Unrec |
Unrec: Unrecorded Rec: Recorded |
Battery Voltage Lo Record |
Auxiliary battery voltage reduction history |
Min.: 0 times Max.: 65535 times |
0 to 65535 times | - |
Battery Control Count (Body ECU) |
Number of auxiliary battery load control operations |
Min.: 0 times Max.: 65535 times |
- | - |
PS Assist Signal | Status of the record of power steering assist signal |
OFF or ON | OFF: Power switch on (IG)
ON: Power switch on (READY) |
- |
Ready Status |
Ready status | OFF or Ready |
OFF: Except power switch on (READY) Ready: Power switch on (READY) |
- |
Motor Actual Current 2 |
Amount of current to motor |
Min.: -327.68 A Max.: 327.67 A |
Value changes in proportion to steering effort |
Power switch on (READY) and steering wheel being turned |
Rotation Angle Sens Avg(SIN) |
Rotation angle sensor average (SIN) |
Min.: 0.0000 V Max.: 4.9725 V |
- | - |
Rotation Angle Sens Avg(COS) |
Rotation angle sensor average (COS) |
Min.: 0.0000 V Max.: 4.9725 V |
- | - |
Motor Overheat Limit Cnt(Normal) |
Number
of times that assist limit was performed according to the estimated
temperature of the motor coil and heat generating components of the
power steering ECU assembly | Min.: 0 times
Max.: 255 times | - |
- |
Assist Limit Cnt(Power Voltage Low) |
Number of times that assist limit was performed due to auxiliary battery voltage having dropped to 9 V or below |
Min.: 0 times Max.: 255 times |
- | - |
Power Vol Low Prevention Limit Cnt |
Number of times that assist limit was performed due to auxiliary battery voltage having dropped to 9.7 V or below |
Min.: 0 times Max.: 255 times |
- | - |
Eng Stall/Ready OFF Cnt |
Number of times that assist limit was performed after the engine stalled and the power switch was turned off |
Min.: 0 times Max.: 255 times |
- | - |
Motor Overheat Limit Cnt(Motor Overload) |
Number
of times that assist limit was performed to prevent the system from
overheating when the motor was overloaded due to the steering wheel
being turned to the full lock position or a tire hitting a curb |
Min.: 0 times Max.: 255 times |
- | - |
Assist Limit Cnt(Vehicle Spd Sig Malf) |
Number
of times that assist power was set to a value suitable for high-speed
driving when high speed is detected due to an abnormal vehicle speed
signal | Min.: 0 times Max.: 255 times |
- | - |
Battery Voltage Keep Limit Cnt |
Number of times that the system was limited to conserve auxiliary battery voltage |
Min.: 0 times Max.: 255 times |
- | - |
Assist Limit Record 1 | Information of assist limit that was used in the past or is currently in use (latest history) |
Unrec, Mtr Overheat, Pow Vol Low, Pow Vol Low Prevent, Eng Stall, Ready OFF, Mtr Overload, Vhcl Spd Sig Malf, Batt Vol Keep |
- | - |
Record 1 Key Cycle | Number of times that the power switch was turned on (IG) before Assist Limit Record 1 was stored |
Min.: 0 times Max.: 65535 times |
- | - |
Record 1 Key Cycle Elapsed Time |
Period of time that elapsed since the power switch was turned on (IG) before Assist Limit Record 1 was stored |
Min.: 0.0 s Max.: 53687091.1 s |
- | - |
Record 1 Power Source | Power source operating status when Assist Limit Record 1 was stored |
No Data, Running, Stop |
- | - |
Assist Limit Record 2 | Information of assist limit that was used in the past (second latest history) |
Unrec, Mtr Overheat, Pow Vol Low, Pow Vol Low Prevent, Eng Stall, Ready OFF, Mtr Overload, Vhcl Spd Sig Malf, Batt Vol Keep |
- | - |
Record 2 Key Cycle | Number
of times that the power switch was turned on (IG) after Assist Limit
Record 2 was stored before Assist Limit Record 1 was stored |
Min.: 0 times Max.: 65535 times |
- | - |
Record 2 Key Cycle Elapsed Time |
Period of time that elapsed since the power switch was turned on (IG) before Assist Limit Record 2 was stored |
Min.: 0.0 s Max.: 53687091.1 s |
- | - |
Record 2 Power Source | Power source operating status when Assist Limit Record 2 was stored |
No Data, Running, Stop |
- | - |
Assist Limit Record 3 | Information of assist limit that was used in the past (third latest history) |
Unrec, Mtr Overheat, Pow Vol Low, Pow Vol Low Prevent, Eng Stall, Ready OFF, Mtr Overload, Vhcl Spd Sig Malf, Batt Vol Keep |
- | - |
Record 3 Key Cycle | Number
of times that the power switch was turned on (IG) after Assist Limit
Record 3 was stored before Assist Limit Record 2 was stored |
Min.: 0 times Max.: 65535 times |
- | - |
Record 3 Key Cycle Elapsed Time |
Period of time that elapsed since the power switch was turned on (IG) before Assist Limit Record 3 was stored |
Min.: 0.0 s Max.: 53687091.1 s |
- | - |
Record 3 Power Source | Power source operating status when Assist Limit Record 3 was stored |
No Data, Running, Stop |
- | - |
Current Key Cycle | Number of times that power switch was turned on (IG) |
Min.: 0 times Max.: 65535 times |
- | - |
Current Key Cycle Elapsed Time |
Time elapsed since power switch was turned on (IG) |
Min.: 0.0 s Max.: 53687091.1 s |
- | - |
Steering Angle | Steering angle |
Min.: -3072.0 deg Max.: 3070.5 deg |
- | - |
Torque Sensor 1 Output |
Torque sensor 1 output value |
Min.: 0.0000 V Max.: 4.9725 V |
- | - |
Torque Sensor 2 Output |
Torque sensor 2 output value |
Min.: 0.0000 V Max.: 4.9725 V |
- | - |
Torque Sensor 1 Power Supply |
Torque sensor 1 power supply voltage |
Min.: 0.0000 V Max.: 4.9725 V |
- | - |
Torque Sensor 2 Power Supply |
Torque sensor 2 power supply voltage |
Min.: 0.0000 V Max.: 4.9725 V |
- | - |
Rotation Angle Sensor Output 1 |
Rotation angle sensor Vx1 output voltage |
Min.: 0.0000 V Max.: 4.9725 V |
- | - |
Rotation Angle Sensor Output 2 |
Rotation angle sensor Vx2 output voltage |
Min.: 0.0000 V Max.: 4.9725 V |
- | - |
Rotation Angle Sensor Output 3 |
Rotation angle sensor Vy1 output voltage |
Min.: 0.0000 V Max.: 4.9725 V |
- | - |
Rotation Angle Sensor Output 4 |
Rotation angle sensor Vy2 output voltage |
Min.: 0.0000 V Max.: 4.9725 V |
- | - |
Motor 1 Terminal Current (U) |
Motor 1 terminal current (U phase) |
Min.: -327.68 A Max.: 327.67 A |
Value changes in proportion to steering effort |
Power switch on (READY) and steering wheel being turned |
Motor 1 Terminal Current (V) |
Motor 1 terminal current (V phase) |
Min.: -327.68 A Max.: 327.67 A |
Value changes in proportion to steering effort |
Power switch on (READY) and steering wheel being turned |
Motor 1 Terminal Current (W) |
Motor 1 terminal current (W phase) |
Min.: -327.68 A Max.: 327.67 A |
Value changes in proportion to steering effort |
Power switch on (READY) and steering wheel being turned |
Motor 2 Terminal Current (U) |
Motor 2 terminal current (U phase) |
Min.: -327.68 A Max.: 327.67 A |
Value changes in proportion to steering effort |
Power switch on (READY) and steering wheel being turned |
Motor 2 Terminal Current (V) |
Motor 2 terminal current (V phase) |
Min.: -327.68 A Max.: 327.67 A |
Value changes in proportion to steering effort |
Power switch on (READY) and steering wheel being turned |
Motor 2 Terminal Current (W) |
Motor 2 terminal current (W phase) |
Min.: -327.68 A Max.: 327.67 A |
Value changes in proportion to steering effort |
Power switch on (READY) and steering wheel being turned |
Motor 1 U Phase Duty | Motor 1 U phase duty |
Min.: 0.00% Max.: 100.00% |
- | - |
Motor 1 V Phase Duty | Motor 1 V phase duty |
Min.: 0.00% Max.: 100.00% |
- | - |
Motor 1 W Phase Duty | Motor 1 W phase duty |
Min.: 0.00% Max.: 100.00% |
- | - |
Motor 2 U Phase Duty | Motor 2 U phase duty |
Min.: 0.00% Max.: 100.00% |
- | - |
Motor 2 V Phase Duty | Motor 2 V phase duty |
Min.: 0.00% Max.: 100.00% |
- | - |
Motor 2 W Phase Duty | Motor 2 W phase duty |
Min.: 0.00% Max.: 100.00% |
- | - |
Motor 1 Terminal Volt (U) |
Motor 1 terminal voltage (U phase) |
Min.: 0.000 V Max.: 98.000 V |
Value changes within 4 to 35 V range |
Power switch on (READY) and steering wheel being turned |
Motor 1 Terminal Volt (V) |
Motor 1 terminal voltage (V phase) |
Min.: 0.000 V Max.: 98.000 V |
Value changes within 4 to 35 V range |
Power switch on (READY) and steering wheel being turned |
Motor 1 Terminal Volt (W) |
Motor 1 terminal voltage (W phase) |
Min.: 0.000 V Max.: 98.000 V |
Value changes within 4 to 35 V range |
Power switch on (READY) and steering wheel being turned |
Motor 2 Terminal Volt (U) |
Motor 2 terminal voltage (U phase) |
Min.: 0.000 V Max.: 98.000 V |
Value changes within 4 to 35 V range |
Power switch on (READY) and steering wheel being turned |
Motor 2 Terminal Volt (V) |
Motor 2 terminal voltage (V phase) |
Min.: 0.000 V Max.: 98.000 V |
Value changes within 4 to 35 V range |
Power switch on (READY) and steering wheel being turned |
Motor 2 Terminal Volt (W) |
Motor 2 terminal voltage (W phase) |
Min.: 0.000 V Max.: 98.000 V |
Value changes within 4 to 35 V range |
Power switch on (READY) and steering wheel being turned |
Motor 1 PIG Power Supply |
Power supply voltage to active motor 1 |
Min.: 0.0000 V Max.: 20.1531 V |
9 to 16 V | Power switch on (READY) and steering wheel being turned |
Motor 2 PIG Power Supply |
Power supply voltage to active motor 2 |
Min.: 0.0000 V Max.: 20.1531 V |
9 to 16 V | Power switch on (READY) and steering wheel being turned |
The Number of DTCs | Number of detected DTCs when freeze frame data was stored |
Min.: 0 Max.: 255 |
0 to 255 | - |
HINT:
- With the vehicle stopped or driving very slowly, if the steering wheel
is turned repeatedly or turned to a lock position and the vehicle is
driven for an extended period of time, the amount of power assist is
decreased to prevent overheating of the motor and ECU. If this occurs,
power switch on (READY) and do not turn the steering wheel for
approximately 10 minutes to improve power assist.
- If the auxiliary battery is not sufficiently charged or the voltage
decreases temporarily, the amount of power assist is reduced and the EPS
warning light comes on. In such cases, the amount of power assist
returns to normal when the auxiliary battery voltage recovers.
Diagnosis System
DIAGNOSIS SYSTEM
CHECK DLC3
(a) Check the DLC3.
Click here
CHECK WARNING LIGHT
(a)
When a problem occurs in the power steering system, the EPS warning
light in the combination meter assembly comes on to inform the driver of
the problem.
Diagnostic Trouble Code Chart
DIAGNOSTIC TROUBLE CODE CHART
Power Steering System
DTC No. | Detection Item |
DTC Detection Condition | Warning Indicate |
Return-to-normal Condition |
Note | Link |
C1511 | Torque Sensor1 |
Torque sensor malfunction |
EPS warning light: Comes on |
Power switch is turned on (IG) again |
- |
|
C1512 | Torque Sensor2 |
Torque sensor malfunction |
EPS warning light: Comes on |
Power switch is turned on (IG) again |
- |
|
C1513 | Torque Sensor Deviation Excessive |
Torque sensor malfunction |
EPS warning light: Comes on |
Power switch is turned on (IG) again |
- |
|
C1514 | Torque Sensor Power Supply Voltage |
Torque sensor malfunction |
EPS warning light: Comes on |
Power switch is turned on (IG) again |
- |
|
C1515 | Torque Sensor Zero Point Adjustment Undone |
This DTC is stored when torque sensor zero point calibration has not been performed. |
EPS warning light: Comes on |
Zero point calibration is performed or the power switch is turned on (IG) again |
There is no malfunction if this DTC is not output again after performing zero point calibration. |
|
C1516 | Torque Sensor Zero Point Adjustment Incomplete |
Torque sensor zero point calibration is incomplete due to the steering wheel being touched during calibration. |
EPS warning light: Comes on |
The DTC is cleared | There
is no malfunction if this DTC is not output again after clearing the
DTC and torque sensor calibration value, and performing zero point
calibration. |
|
C1517 | Torque Hold |
Torque sensor malfunction |
EPS warning light: Comes on |
Power switch is turned on (IG) again |
- |
|
C1521 | Short in Motor Circuit |
Motor overcurrent | EPS warning light: Comes on |
Power switch is turned on (IG) again |
- |
|
C1522 | Power Supply Sensor |
Motor current sensor malfunction |
EPS warning light: Comes on |
Power switch is turned on (IG) again |
- |
|
C1523 | Current Deviation Excessive |
Excessively large current deviation |
EPS warning light: Comes on |
Power switch is turned on (IG) again |
- |
|
C1528 | Motor Rotation Angle Sensor |
Motor rotation angle sensor malfunction |
EPS warning light: Comes on |
Power switch is turned on (IG) again |
- |
|
C1531 | ECU Malfunction |
ECU internal malfunction (CPU malfunction) |
EPS warning light: Comes on |
Power switch is turned on (IG) again |
- |
|
C1532 | ECU Malfunction |
ECU internal malfunction (Peripheral circuit malfunction) |
EPS warning light: Comes on |
Power switch is turned on (IG) again |
- |
|
C1533 | Temperature Sensor Circuit is Low or High |
ECU internal malfunction (Substrate temperature sensor malfunction) |
EPS warning light: Comes on |
The ECU judges the system has returned to normal |
- |
|
C1534 | EEPROM |
ECU internal malfunction (EEPROM error) |
EPS warning light: Comes on |
Power switch is turned on (IG) again |
- |
|
C1541 | Vehicle Speed Signal |
A vehicle speed signal malfunction is detected |
EPS warning light: Comes on |
The ECU judges the system has returned to normal |
- |
|
C1551 | IG Power Supply Voltage |
When the PIG power supply voltage is normal, the IG power supply voltage is 18.5 V or higher |
EPS warning light: Comes on |
The ECU judges the system has returned to normal |
- |
|
C1552 | PIG Power Supply Voltage |
PIG power source circuit malfunction |
EPS warning light: Comes on |
Power switch is turned on (IG) again |
- |
|
C1554 | Power Supply Relay Failure |
Power source relay circuit malfunction |
EPS warning light: Comes on |
Power switch is turned on (IG) again |
- |
|
C1555 | Motor Relay Welding Failure |
Motor relay circuit malfunction |
EPS warning light: Comes on |
Power switch is turned on (IG) again |
- |
|
C1567 | Error in Matching of ECUs |
- An incompatible hybrid vehicle control ECU is detected
- An incompatible main body ECU (multiplex network body ECU) is detected
- An incompatible skid control ECU (brake booster with master cylinder assembly) is detected
| EPS warning light: Comes on |
The ECU judges the system has returned to normal or the power switch is turned on (IG) again |
- |
|
C1581 | Assist Map Number Un-Writing |
Assist map not written in power steering ECU (rack and pinion power steering gear assembly) |
EPS warning light: Comes on |
Assist Map Writing is performed or the power switch is turned on (IG) again |
- |
|
C1582 | Assist Map Number Mismatch |
Assist map number mismatch |
EPS warning light: Does not come on |
Assist Map Writing is performed or the power switch is turned on (IG) again |
- |
|
U0126 | Lost Communication With Steering Angle Sensor Module |
Lost communication with steering angle sensor |
EPS warning light: Comes on |
The ECU judges the system has returned to normal or the power switch is turned on (IG) again |
- |
|
U0129 | Lost Communication with Brake System Control Module |
Lost communication with skid control ECU (Brake booster with master cylinder assembly) |
EPS warning light: Comes on |
The ECU judges the system has returned to normal or the power switch is turned on (IG) again |
- |
|
U023A | Lost Communication with Front Camera Module |
Lost communication with forward recognition camera |
EPS warning light: Does not come on |
The ECU judges the system has returned to normal or the power switch is turned on (IG) again |
- |
|
U0293 | Lost Communication with Hybrid Control Module |
Lost communication with hybrid vehicle control ECU |
EPS warning light: Does not come on |
The ECU judges the system has returned to normal or the power switch is turned on (IG) again |
- |
|
Dtc Check / Clear
DTC CHECK / CLEAR
CHECK DTCs (USING TECHSTREAM)
(a) Turn the power switch off.
(b) Connect the Techstream to the DLC3.
(c) Turn the power switch on (IG).
(d) Turn the Techstream on.
(e) Enter the following menus: Chassis / EMPS / Trouble Codes.
Chassis > EMPS > Trouble Codes
(f) Check the details of the DTCs.
Click here
CHECK DTCs (USING SST CHECK WIRE)
(a) Using SST, connect terminals 13 (TC) and 4 (CG) of the DLC3.
SST: 09843-18040
(b) Turn the power switch on (IG).
(c)
Read and write down any DTCs indicated by the blinking of the EPS
warning light in the combination meter assembly. Refer to the
illustration to the right for examples of the normal system code and
DTCs 21 and 22.
*a | Normal System Code |
*b | Codes 21 and 22 |
*c | ON |
*d | OFF |
*e | Seconds |
*f | Code 21 |
*g | Code 22 |
HINT:
- If the EPS warning light does not blink to display stored DTCs or the
normal system code, inspect the circuit shown in the table below.
Trouble Area |
Link |
EPS warning light circuit |
|
- If two or more malfunctions are detected simultaneously, DTCs will be displayed in ascending numerical order.
(d) Refer to Diagnostic Trouble Code Chart for DTC information.
Click here
(e) Check the details of the DTCs.
EPS DTC
EPS Warning Light Display |
Tester Display |
11 | C1511 |
C1512 |
C1513 |
C1514 |
C1517 |
12 | C1528 |
13 | C1541 |
15 | C1515 |
16 | C1516 |
22 | C1552 |
23 | C1554 |
24 | C1521 |
C1522 |
C1523 |
25 | C1531 |
C1532 |
C1533 |
C1534 |
C1551 |
C1555 |
26 | C1581 |
C1582 |
41 |
U0100 |
42 |
U0129 |
44 |
C1567 |
45 |
U023A |
47 |
U0126 |
CLEAR DTCs (USING TECHSTREAM)
(a) Turn the power switch off.
(b) Connect the Techstream to the DLC3.
(c) Turn the power switch on (IG).
(d) Turn the Techstream on.
(e) Enter the following menus: Chassis / EMPS / Trouble Codes.
Chassis > EMPS > Trouble Codes
(f) Clear the DTCs.
Chassis > EMPS > Clear DTCs (g) Turn the power switch off.
(h) Disconnect the Techstream from the DLC3.
EPS Warning Light Circuit
CAUTION / NOTICE / HINT
NOTICE:
- Perform this troubleshooting procedure when no DTCs are output, including DTCs related to CAN communication system malfunctions.
- If the customer reports that the steering feels heavy, refer to the "Heavy steering" item in the Problem Symptoms Table.
Click here
PROCEDURE
1. | INSPECT COMBINATION METER ASSEMBLY |
(a) Perform the Active Test of the combination meter assembly using the Techstream.
Click here
Body Electrical > Combination Meter > Active Test
Tester Display |
EPS Warning |
(b) Check the combination meter assembly.
OK:
The EPS warning light turns on or off in accordance with the Techstream operation.
OK |
| REPLACE RACK AND PINION POWER STEERING GEAR ASSEMBLY |
NG |
| GO TO METER / GAUGE SYSTEM |
Fail-safe Chart
FAIL-SAFE CHART
If a
problem occurs in the power steering system, the power steering assist
will be stopped or the amount of power assist will be decreased to
protect the system.
Power Steering System
Malfunction | Fail-safe Operation |
EPS warning light | Buzzer |
- Torque sensor (rack and pinion power steering gear assembly) malfunction
- Power steering motor (rack and pinion power steering gear assembly) malfunction
- Power steering ECU (rack and pinion power steering gear assembly) malfunction
| Power steering assist stops or assist amount is limited |
Red or yellow | Sounds intermittently or once |
- Vehicle speed signal malfunction
- Skid control ECU (brake booster with master cylinder assembly) malfunction
- History of power steering ECU (rack and pinion power steering gear assembly) overheating
- History of decrease in battery voltage (not malfunction)
| Power steering assist is temporarily limited |
Yellow | Sounds once |
HINT:
- If the power steering assist stops, the EPS warning light comes on (red).
- If the amount of power assist is reduced, the EPS warning light comes on (yellow) and a vibration or sound may occur.
- The amount of power assist may be decreased to prevent the motor and
ECUs from overheating if the steering wheel is continuously turned when
the vehicle is either stopped or driven at a low speed, or if the
steering wheel is kept at either full lock position for a long time. In
such cases, the amount of power assist returns to normal if the steering
wheel is not turned for approximately 10 minutes with the power switch
on (READY).
- If the auxiliary battery is not sufficiently charged or the voltage
decreases temporarily, the amount of power assist will be reduced and
the EPS warning light will come on. In such cases, the amount of power
assist returns to normal when the auxiliary battery voltage recovers.
Freeze Frame Data
FREEZE FRAME DATA
FREEZE FRAME DATA
NOTICE:
- It is difficult to show the specified values (judgment values) clearly
because freeze frame data values change significantly due to differences
in measurement conditions, surroundings, or vehicle conditions. For
this reason, there may be a problem even when the values are within
specification.
- Turn the power switch on (IG) and park the vehicle on level ground. Check the freeze frame data by using the Techstream.
(a) Turn the power switch off.
(b) Connect the Techstream to the DLC3.
(c) Turn the power switch on (IG).
(d) Turn the Techstream on.
(e) Check the freeze frame data on the Techstream.
Chassis > EMPS
Tester Display | Measurement Item |
Range | Normal Condition |
Diagnostic Note |
Meter Vehicle Velocity |
Vehicle speed from speedometer |
Min.: 0.0 km/h (0.0 MPH) Max.: 300.0 km/h (186.4 MPH) |
- 0 km/h (0 MPH): Power switch on (READY) and vehicle stopped
- No significant fluctuation: Power switch on (READY) and vehicle driven at a constant speed
| - |
Wheel Speed Right | Rear right wheel speed |
Min.: 0 km/h (0 MPH) Max.: 255 km/h (158 MPH) |
- 0 km/h (0 MPH): Power switch on (READY) and vehicle stopped
- No significant fluctuation: Power switch on (READY) and vehicle driven at a constant speed
| - |
Wheel Speed Left | Rear left wheel speed |
Min.: 0 km/h (0 MPH) Max.: 255 km/h (158 MPH) |
- 0 km/h (0 MPH): Power switch on (READY) and vehicle stopped
- No significant fluctuation: Power switch on (READY) and vehicle driven at a constant speed
| - |
Motor Actual Current | Amount of current to motor |
Min.: -327.68 A Max.: 327.67 A |
Value changes in proportion to steering effort - The value increases when turning right and decreases when turning left |
Power switch on (READY) and steering wheel being turned |
Command Value Current | Requested current to motor |
Min.: -327.68 A Max.: 327.67 A |
Value changes in proportion to steering effort - The value increases when turning right and decreases when turning left |
Power switch on (READY) and steering wheel being turned |
Steering Angle Velocity |
Steering angle speed | Min.: -32768 deg/s
Max.: 32767 deg/s | Value changes in proportion to steering speed
- The value increases when turning left and decreases when turning right |
Power switch on (READY) and steering wheel being turned |
Thermistor Temperature |
ECU substrate temperature |
Min.: -50.0°C (-58.0°F) Max.: 150.0°C (302.0°F) |
-50°C to 150°C (-58°F to 302°F) |
- |
IG Power Supply |
IG power source voltage |
Min.: 0.0000 V Max.: 20.1531 V |
8 to 16 V | Power switch on (IG) |
Steering Wheel Torque | Steering wheel torque |
Min.: -327.68 Nm Max.: 7.00 Nm |
Value changes in proportion to steering effort - The value increases when turning left and decreases when turning right |
Power switch on (READY) and steering wheel being turned |
Motor Rotation Angle | Motor rotation angle |
Min.: 0.000 deg Max.: 1441.770 deg |
During steering operation, motor rotation angle value changes from 0 to 360° |
Power switch on (READY) and steering wheel being turned |
Command Val Current 2 | Requested current to motor |
Min.: -327.68 A Max.: 327.67 A |
Value changes in proportion to steering effort |
Power switch on (READY) and steering wheel being turned |
Motor Voltage | Motor power supply voltage |
Min.: 0.000 V Max.: 98.000 V |
- Approximately 27 V: Power switch on (READY) and steering wheel being turned
- Approximately 27 to 34 V: Power switch on (READY) and steering wheel not being turned
| - |
TRQ1 Zero Point Value | Zero point value of torque sensor 1 |
Min.: 0.0000 V Max.: 4.9725 V |
2.3 to 2.7 V | Power switch on (READY) and steering wheel not being turned (without load) |
TRQ2 Zero Point Value | Zero point value of torque sensor 2 |
Min.: 0.0000 V Max.: 4.9725 V |
2.3 to 2.7 V | Power switch on (READY) and steering wheel not being turned (without load) |
PS Assist Signal | Status of the record of power steering assist signal |
OFF or ON | OFF: Power switch on (IG)
ON: Power switch on (READY) |
- |
Ready Status |
Ready status | OFF or Ready |
OFF: Except power switch on (READY) Ready: Power switch on (READY) |
- |
Motor Actual Current 2 |
Amount of current to motor |
Min.: -327.68 A Max.: 327.67 A |
Value changes in proportion to steering effort |
Power switch on (READY) and steering wheel being turned |
Rotation Angle Sens Avg(SIN) |
Rotation angle sensor average (SIN) |
Min.: 0.0000 V Max.: 4.9725 V |
- | - |
Rotation Angle Sens Avg(COS) |
Rotation angle sensor average (COS) |
Min.: 0.0000 V Max.: 4.9725 V |
- | - |
Steering Angle | Steering angle |
Min.: -3072.0 deg Max.: 3070.5 deg |
- | - |
Torque Sensor 1 Output |
Torque sensor 1 output value |
Min.: 0.0000 V Max.: 4.9725 V |
- | - |
Torque Sensor 2 Output |
Torque sensor 2 output value |
Min.: 0.0000 V Max.: 4.9725 V |
- | - |
Torque Sensor 1 Power Supply |
Torque sensor 1 power supply voltage |
Min.: 0.0000 V Max.: 4.9725 V |
- | - |
Torque Sensor 2 Power Supply |
Torque sensor 2 power supply voltage |
Min.: 0.0000 V Max.: 4.9725 V |
- | - |
Rotation Angle Sensor Output 1 |
Rotation angle sensor Vx1 output voltage |
Min.: 0.0000 V Max.: 4.9725 V |
- | - |
Rotation Angle Sensor Output 2 |
Rotation angle sensor Vx2 output voltage |
Min.: 0.0000 V Max.: 4.9725 V |
- | - |
Rotation Angle Sensor Output 3 |
Rotation angle sensor Vy1 output voltage |
Min.: 0.0000 V Max.: 4.9725 V |
- | - |
Rotation Angle Sensor Output 4 |
Rotation angle sensor Vy2 output voltage |
Min.: 0.0000 V Max.: 4.9725 V |
- | - |
Motor 1 Terminal Current (U) |
Motor 1 terminal current (U phase) |
Min.: -327.68 A Max.: 327.67 A |
Value changes in proportion to steering effort |
Power switch on (READY) and steering wheel being turned |
Motor 1 Terminal Current (V) |
Motor 1 terminal current (V phase) |
Min.: -327.68 A Max.: 327.67 A |
Value changes in proportion to steering effort |
Power switch on (READY) and steering wheel being turned |
Motor 1 Terminal Current (W) |
Motor 1 terminal current (W phase) |
Min.: -327.68 A Max.: 327.67 A |
Value changes in proportion to steering effort |
Power switch on (READY) and steering wheel being turned |
Motor 2 Terminal Current (U) |
Motor 2 terminal current (U phase) |
Min.: -327.68 A Max.: 327.67 A |
Value changes in proportion to steering effort |
Power switch on (READY) and steering wheel being turned |
Motor 2 Terminal Current (V) |
Motor 2 terminal current (V phase) |
Min.: -327.68 A Max.: 327.67 A |
Value changes in proportion to steering effort |
Power switch on (READY) and steering wheel being turned |
Motor 2 Terminal Current (W) |
Motor 2 terminal current (W phase) |
Min.: -327.68 A Max.: 327.67 A |
Value changes in proportion to steering effort |
Power switch on (READY) and steering wheel being turned |
Motor 1 U Phase Duty | Motor 1 U phase duty |
Min.: 0.00% Max.: 100.00% |
- | - |
Motor 1 V Phase Duty | Motor 1 V phase duty |
Min.: 0.00% Max.: 100.00% |
- | - |
Motor 1 W Phase Duty | Motor 1 W phase duty |
Min.: 0.00% Max.: 100.00% |
- | - |
Motor 2 U Phase Duty | Motor 2 U phase duty |
Min.: 0.00% Max.: 100.00% |
- | - |
Motor 2 V Phase Duty | Motor 2 V phase duty |
Min.: 0.00% Max.: 100.00% |
- | - |
Motor 2 W Phase Duty | Motor 2 W phase duty |
Min.: 0.00% Max.: 100.00% |
- | - |
Motor 1 Terminal Volt (U) |
Motor 1 terminal voltage (U phase) |
Min.: 0.000 V Max.: 98.000 V |
Value changes within 4 to 35 V range |
Power switch on (READY) and steering wheel being turned |
Motor 1 Terminal Volt (V) |
Motor 1 terminal voltage (V phase) |
Min.: 0.000 V Max.: 98.000 V |
Value changes within 4 to 35 V range |
Power switch on (READY) and steering wheel being turned |
Motor 1 Terminal Volt (W) |
Motor 1 terminal voltage (W phase) |
Min.: 0.000 V Max.: 98.000 V |
Value changes within 4 to 35 V range |
Power switch on (READY) and steering wheel being turned |
Motor 2 Terminal Volt (U) |
Motor 2 terminal voltage (U phase) |
Min.: 0.000 V Max.: 98.000 V |
Value changes within 4 to 35 V range |
Power switch on (READY) and steering wheel being turned |
Motor 2 Terminal Volt (V) |
Motor 2 terminal voltage (V phase) |
Min.: 0.000 V Max.: 98.000 V |
Value changes within 4 to 35 V range |
Power switch on (READY) and steering wheel being turned |
Motor 2 Terminal Volt (W) |
Motor 2 terminal voltage (W phase) |
Min.: 0.000 V Max.: 98.000 V |
Value changes within 4 to 35 V range |
Power switch on (READY) and steering wheel being turned |
Motor 1 PIG Power Supply |
Power supply voltage to active motor 1 |
Min.: 0.0000 V Max.: 20.1531 V |
9 to 16 V | Power switch on (READY) and steering wheel being turned |
Motor 2 PIG Power Supply |
Power supply voltage to active motor 2 |
Min.: 0.0000 V Max.: 20.1531 V |
9 to 16 V | Power switch on (READY) and steering wheel being turned |
How To Proceed With Troubleshooting
CAUTION / NOTICE / HINT
HINT:
- Use the following procedure to troubleshoot the power steering system.
- *: Use the Techstream.
PROCEDURE
1. | VEHICLE BROUGHT TO WORKSHOP |
NEXT |
| |
2. |
INSPECT AUXILIARY BATTERY |
(a) Turn the power switch off.
(b) Measure the voltage of the auxiliary battery.
Standard Voltage:
11 to 14 V
HINT:
If the voltage is below 11 V, recharge or replace the auxiliary battery before proceeding to the next step.
NEXT |
| |
3. |
CHECK DTC AND FREEZE FRAME DATA* |
HINT:
Refer to DTC Check / Clear.
Chassis > EMPS > Trouble Codes
NEXT |
| |
4. |
PROBLEM SYMPTOM CONFIRMATION |
Result | Proceed to |
Symptom does not occur. |
A |
Symptom occurs. |
B |
B |
| GO TO STEP 6 |
A |
| |
NEXT |
| |
6. |
CHECK CAN COMMUNICATION SYSTEM* |
(a) Check for DTCs.
Click here
Result | Proceed to |
CAN communication system DTCs are not output. |
A |
CAN communication system DTCs are output. |
B |
HINT:
- If any CAN communication system DTCs are output, perform troubleshooting for the CAN communication system first.
- If communication to the rack and pinion power steering gear assembly
cannot be established through the Techstream, inspect terminals CANH and
CANL of the DLC3 and the rack and pinion power steering gear assembly,
and the IG circuit of the rack and pinion power steering gear assembly.
B |
| PROCEED TO CAN COMMUNICATION SYSTEM |
A |
| |
(a) Check for DTCs.
Chassis > EMPS > Trouble Codes
HINT:
Refer to Diagnostic Trouble Code Chart when any DTCs are output.
Click here
Result | Proceed to |
DTCs are not output. |
A |
DTCs are output. |
B |
B |
| GO TO STEP 10 |
A |
| |
8. |
PROBLEM SYMPTOMS TABLE |
(a) Refer to Problem Symptoms Table.
Click here
Result | Proceed to |
Fault is not listed in Problem Symptoms Table. |
A |
Fault is listed in Problem Symptoms Table. |
B |
B |
| GO TO STEP 10 |
A |
| |
9. |
OVERALL ANALYSIS AND TROUBLESHOOTING* |
(a) Refer to Terminals of ECU.
Click here
(b) Refer to Data List / Active Test.
Click here
NEXT |
| |
NEXT |
| |
NEXT |
| END |
On-vehicle Inspection
ON-VEHICLE INSPECTION
PROCEDURE
1. CHECK STEERING EFFORT (TORQUE)
NOTICE:
These
service operations may affect the SRS airbags. Be sure to read the
precautionary notices concerning the SRS airbag system before servicing.
Click here
(a) Stop the vehicle on a level, paved surface and align the wheels straight ahead.
(b) Remove the horn button assembly.
Click here
(c) Connect the cable to the negative (-) auxiliary battery terminal.
(d) Using a torque wrench, check that the steering wheel set bolt is properly tightened.
Torque:
62 N·m {632 kgf·cm, 46 ft·lbf}
(e) Turn the power switch on (READY) so that the power steering is ready to operate.
(f)
Turn the steering wheel 90 degrees to the right and check steering
effort (torque) with the steering wheel turned. Check in the opposite
direction using the same method.
Standard Steering Effort (Reference):
5.5 N*m (56 kgf*cm, 49 in.*lbf) or less
(g) Align the front wheels facing straight ahead.
(h) Turn the power switch off.
(i) Disconnect the cable from the negative (-) auxiliary battery terminal.
NOTICE:
When disconnecting the cable, some systems need to be initialized after the cable is reconnected.
Click here
(j) Install the horn button assembly.
Click here
Parts Location
PARTS LOCATION
ILLUSTRATION
*1 | FORWARD RECOGNITION CAMERA |
*2 | BRAKE BOOSTER WITH MASTER CYLINDER ASSEMBLY
- SKID CONTROL ECU |
*3 | RACK AND PINION POWER STEERING GEAR ASSEMBLY
- POWER STEERING ECU -POWER STEERING MOTOR -TORQUE SENSOR |
*4 | NO. 1 ENGINE ROOM RELAY BLOCK AND NO. 1 JUNCTION BLOCK ASSEMBLY
- EPS FUSE |
*5 | COMBINATION METER ASSEMBLY |
*6 | HYBRID VEHICLE CONTROL ECU |
*7 | MAIN BODY ECU (MULTIPLEX NETWORK BODY ECU) |
*8 | INSTRUMENT PANEL JUNCTION BLOCK ASSEMBLY
- IG1-NO. 1 RELAY - EPS-IG1 FUSE |
*9 | DLC3 |
*10 | AIR CONDITIONING AMPLIFIER ASSEMBLY |
*11 | STEERING SENSOR |
- | - |
Precaution
PRECAUTION
PRECAUTION FOR DISCONNECTING CABLE FROM NEGATIVE AUXILIARY BATTERY TERMINAL
NOTICE:
When
disconnecting the cable from the negative (-) auxiliary battery
terminal, initialize the following system(s) after the cable is
reconnected.
System | Procedure |
Lane Departure Alert System (w/ Steering Control) |
|
Pre-collision System |
Intelligent Clearance Sonar System |
Lighting System (for HV Model with Cornering Light) |
Parking Assist Monitor System |
Panoramic View Monitor System |
HANDLING PRECAUTIONS FOR SRS AIRBAG SYSTEM
(a)
This vehicle is equipped with a Supplemental Restraint System (SRS).
Failure to carry out service operations in the correct sequence could
cause the SRS to unexpectedly deploy during servicing. This may cause a
serious accident.
Before servicing (including
inspection, replacement, removal and installation of parts), be sure to
read the precautionary notices for the Supplemental Restraint System.
Click here
PRECAUTIONS FOR REMOVAL, INSTALLATION AND REPLACEMENT OF ELECTRONIC POWER STEERING COMPONENTS
(a)
Be sure to align the front wheels straight ahead when removing and
installing the rack and pinion power steering gear assembly.
(b) When disconnecting the steering intermediate shaft assembly, be sure to place matchmarks before starting the operation.
(c) After replacing the rack and pinion power steering gear assembly, calibrate the torque sensor zero point.
Click here
HANDLING PRECAUTION
(a) When handling electronic parts:
(1)
Do not subject any parts such as ECUs and relays to any impact. Replace
them with new ones if dropped or subjected to a strong impact.
(2) Do not expose any electronic parts to high temperatures or humidity.
(3) In order to prevent deformation or malfunctions due to static electricity, do not touch the connector terminals.
(b) When handling the rack and pinion power steering gear assembly:
(1)
When replacing the power steering ECU (rack and pinion power steering
gear assembly), make sure to replace each rack and pinion power steering
gear assembly with a new one.
NOTICE:
Do not use a rack and pinion power steering gear assembly intended from another vehicle (demo models, etc.).
(2)
Do not subject the rack and pinion power steering gear assembly to any
strong impact (particularly the motor and torque sensor). Replace these
parts with new ones if dropped or subjected to any severe impact.
(3) Do not pull the harness when carrying the rack and pinion power steering gear assembly.
(4)
When the rack and pinion power steering gear assembly has been
replaced, perform assist map writing and torque sensor zero point
calibration.
Click here
PRECAUTIONS FOR CAN COMMUNICATION
(a)
CAN communication lines are used to receive information from the skid
control ECU (brake booster with master cylinder assembly) and ECM and to
transmit warnings to the combination meter assembly. When problems are
detected in the CAN communication lines, CAN communication DTCs are
stored.
(b) If any CAN communication system DTCs are output, perform troubleshooting for the CAN communication system first.
(c)
The wiring used for each communication line is a twisted pair of wires
that have an equal length. Do not temporarily repair a CAN communication
line with a bypass wire or equivalent.
Problem Symptoms Table
PROBLEM SYMPTOMS TABLE
HINT:
- Use the table below to help determine the cause of problem symptoms. If
multiple suspected areas are listed, the potential causes of the
symptoms are listed in order of probability in the "Suspected Area"
column of the table.
- Check each symptom by checking the suspected areas in the order they are listed. Replace parts as necessary.
- Inspect the fuses and relays related to this system before inspecting the suspected areas below.
Power Steering System
Symptom | Suspected Area |
Link |
Heavy steering | Check assist limit record |
|
Front tires (improperly inflated, unevenly worn) |
|
Front wheel alignment (incorrect) |
|
Front suspension (Lower ball joint) |
|
Rack and pinion power steering gear assembly |
|
Steering effort differs between right and left or is uneven |
Rotation angle sensor initialization and torque sensor zero point calibration incomplete |
|
Front tires (improperly inflated, unevenly worn) |
|
Front wheel alignment (incorrect) |
|
Front suspension (Lower ball joint) |
|
Rack and pinion power steering gear assembly |
|
Steering column assembly (for Manual Tilt and Manual Telescopic Steering Column) |
|
Steering column assembly (for Power Tilt and Power Telescopic Steering Column) |
|
While
driving, steering effort does not change in accordance with vehicle
speed, or steering wheel does not return to its centered position easily |
Skid control ECU (Brake Booster with Master Cylinder Assembly) |
|
Speed sensor |
|
Rack and pinion power steering gear assembly |
|
CAN communication system |
|
Friction sounds occur when turning steering wheel during low speed driving |
Rack and pinion power steering gear assembly |
|
Steering column assembly (for Manual Tilt and Manual Telescopic Steering Column) |
|
Steering column assembly (for Power Tilt and Power Telescopic Steering Column) |
|
Spiral with cable sensor sub-assembly |
|
Steering column cover contacting steering wheel assembly (for Manual Tilt and Manual Telescopic Steering Column) |
|
Steering column cover contacting steering wheel assembly (for Power Tilt and Power Telescopic Steering Column) |
|
High-pitched sound (squeaking) occurs when turning steering wheel slowly with vehicle stopped |
Rack and pinion power steering gear assembly |
|
Steering wheel installation (incorrect) |
|
Steering wheel vibrates and noise occurs when turning steering wheel from lock to lock |
Rack and pinion power steering gear assembly |
|
Steering column assembly (for Manual Tilt and Manual Telescopic Steering Column) |
|
Steering column assembly (for Power Tilt and Power Telescopic Steering Column) |
|
Steering wheel installation (incorrect) |
|
EPS warning light remains on | EPS warning light circuit |
|
System Description
SYSTEM DESCRIPTION
DESCRIPTION
(a)
The power steering ECU (rack and pinion power steering gear assembly)
generates the necessary steering assist torque by calculating the
steering assist force and controlling the motor current, based on the
steering torque information from the torque sensor (rack and pinion
power steering gear assembly), vehicle speed information from the skid
control ECU (brake booster with master cylinder assembly), and
information from the ECUs.
(b) When there is a drop
in the power source voltage, the rear window defogger, windshield
deicer, outer mirror heater, PTC heater and seat heater operations are
limited as part of power steering system load control.
(c)
When there is a drop in the power source that may require an increase
in steering force, the system illuminates the power steering warning
light in order to warn the driver.
Function of Components:
Component | Function |
Rack and Pinion Power Steering Gear Assembly HINT: The components listed on the right are built-in |
Power Steering ECU |
- Calculates the motor operation current based on the steering torque and vehicle speed signals, and outputs it to the motor.
- When a malfunction is detected in the power steering system, it outputs a warning signal to the combination meter assembly.
|
Power Steering Motor |
- Generates power assist in accordance with the actuation current received from the power steering ECU.
- The built-in motor rotation angle sensor detects the rotation angle of the motor.
|
Torque Sensor |
Detects the steering torque. |
Reduction Mechanism | Decelerates the motor rotation torque and transmits it to the rack shaft. |
Steering Sensor | Detects the steering angle and steering direction. |
Skid Control ECU (Brake Booster with Master Cylinder Assembly) |
Sends
the vehicle speed signal and steering coordinated control amount signal
to the rack and pinion power steering gear assembly. |
Hybrid Vehicle Control ECU |
Transmits the READY signal to the power steering ECU (rack and pinion power steering gear assembly). |
Air Conditioning Amplifier Assembly |
Receives a signal from the power steering ECU (rack and pinion power steering gear assembly) to limit electrical usage. |
Combination Meter Assembly |
EPS Warning Light | Illuminates
to alert the driver when the power steering ECU (rack and pinion power
steering gear assembly) detects a malfunction in the power steering
system. |
Multi-information Display |
Displays a warning message to inform the driver of a malfunction in the system. |
Master Warning Light | Illuminates when a warning message is displayed on the multi-information display. |
Multi Buzzer | Sounds to warn the driver of a malfunction in the system. |
Forward Recognition Camera |
Requests steering assist torque when the lane departure alert system judges that the vehicle is departing from its lane. |
System Diagram
SYSTEM DIAGRAM
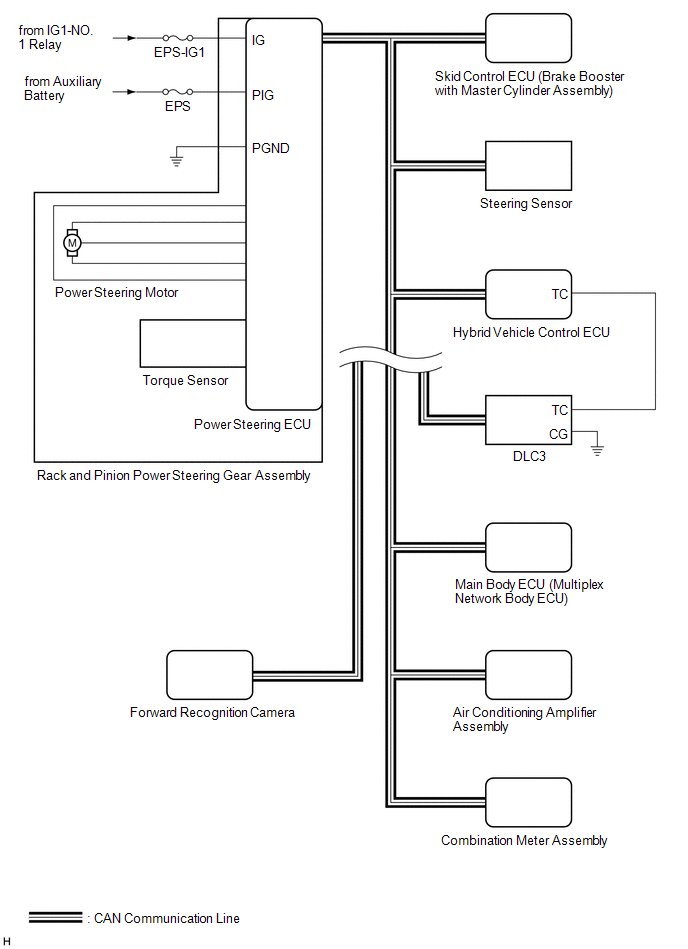
Terminals Of Ecu
TERMINALS OF ECU
TERMINALS OF ECU
*a | Component without harness connected
(Rack and Pinion Power Steering Gear Assembly) |
- | - |
HINT:
- The rack and pinion power steering gear assembly uses waterproof
connectors. Therefore, voltage or waveforms cannot be checked with the
connectors connected to the vehicle.
- Use the Data List and Active Test on the Techstream to check the
operation of the rack and pinion power steering gear assembly and check
that communication is established.
Click here
Terminal No. (Symbol) | Terminal Description |
C67-4 (IG) | IG power source |
C67-7 (PGND) | power ground |
C67-8 (PIG) | power source |
C67-10 (CANH) | CAN communication line |
C67-11 (CANL) | CAN communication line |
CHECK WIRE HARNESS SIDE CONNECTOR
*a | Front view of wire harness connector
(to Rack and Pinion Power Steering Gear Assembly) |
- | - |
(a) Disconnect the C67 rack and pinion power steering gear assembly.
(b) Measure the voltage and resistance according to the value(s) in the table below.
Terminal No. (Symbol) | Wiring Color |
Terminal Description | Condition |
Specified Condition |
C67-4 (IG) - Body ground |
W - Body ground | IG power source |
Power switch on (IG) |
8 to 16 V |
C67-7 (PGND) - Body ground |
B - Body ground | power ground |
Always | Below 1 Ω |
C67-8 (PIG) - Body ground |
W - Body ground | power source |
Always | 9 to 16 V |
Lost Communication With Steering Angle Sensor Module (U0126,U0129,U023A,U0293)
DESCRIPTION
The power
steering ECU (rack and pinion power steering gear assembly) receives
signals from the hybrid vehicle control ECU, steering sensor, skid
control ECU (brake booster with master cylinder assembly) and forward
recognition camera via CAN communication.
DTC No. | Detection Item |
DTC Detection Condition | Trouble Area |
Warning Indicate | Return-to-normal Condition |
Note |
U0126 |
Lost Communication With Steering Angle Sensor Module |
Lost communication with steering angle sensor |
- CAN communication system
- Steering angle sensor
- Rack and pinion power steering gear assembly
| EPS warning light: Comes on |
The ECU judges the system has returned to normal or the power switch is turned on (IG) again |
- |
U0129 |
Lost Communication with Brake System Control Module |
Lost communication with skid control ECU (Brake booster with master cylinder assembly) |
- CAN communication system
- Skid control ECU (Brake booster with master cylinder assembly)
- Rack and pinion power steering gear assembly
| EPS warning light: Comes on |
The ECU judges the system has returned to normal or the power switch is turned on (IG) again |
- |
U023A |
Lost Communication with Front Camera Module |
Lost communication with forward recognition camera |
- CAN communication system
- Forward recognition camera
- Rack and pinion power steering gear assembly
| EPS warning light: Does not come on |
The ECU judges the system has returned to normal or the power switch is turned on (IG) again |
- |
U0293 |
Lost Communication with Hybrid Control Module |
Lost communication with hybrid vehicle control ECU |
- CAN communication system
- Hybrid vehicle control ECU
| EPS warning light: Does not come on |
The ECU judges the system has returned to normal or the power switch is turned on (IG) again |
- |
PROCEDURE
1. |
GO TO CAN COMMUNICATION SYSTEM |
(a) Go to CAN communication system.
Click here
NEXT |
| END |